Parts damaged from high temperature or poorly overheated joints, the short lifetime of tips and soldering handles, poor solder spillage, … Sounds familiar? Here are the answers to frequently asked questions and difficulties regarding manual soldering.
Hand soldering is basically quite a simple operation - at least at first sight. It is true that nice and good connections can be made, after a short training, even by a person who has never held a soldering iron before. But you, who daily solder various-sized joints, parts and materials, know that it is often almost a masterpiece to achieve a reliable and visually appealing joint.
Whether it is a prototype, a pre-production series or a run-in production, a reliable connection is crucial at all stages of the project.
What is a soldered joint?
It is an electrically conductive connection of two wires, surfaces, outlets, leads/pins, etc. using molten metal. This connection, in the vast majority of cases, also has a fastening function where it mechanically fixes the component or conductor, and therefore, except applications operating at a high vibration, the components no longer require additional support.
Without deep penetration into chemistry, metallurgy, and exploration of the properties of metals, we can conclude that molten solder (colloidal tin) forms an intermetallic transition layer that contains elements of the solder itself, as well as elements contained in the soldered surface, most often copper.
Solder

Solders are divided into so-called soft and hard. However, this classification is not about mechanical hardness or softness. It is about the melting temperature of the solder. Soft solders have a melting point below 500 °C and in electronics, we use almost exclusively soft soldering.
Soft solders are practically always made up of two to three main metals and additives. In a very small proportion, they also contain various micro-alloying ingredients, the ingredients of which are usually hidden by the manufacturer, as they are part of the manufacturing know-how and often have a significant impact on the solder behaviour.
Historically, the most widely used were tin/lead (SnPb) solders for many decades, most often in a ratio of 60:40 or Sn63Pb37, etc., and a small amount of additional metals such as copper and other micro-alloying ingredients.
However, lead has one major and well-known drawback - it is a toxic heavy metal, accumulating in the body, attacking the nerve system, but also reproductive organs, etc. So, after the adoption of the directive, known as RoHS, lead has been abandoned (except for several segments such as medicine, military and automotive).
Although the transition to lead-free technology has brought technological complications, overall, it has been a very good environmental step.
Why complications with "lead-free"?
With this transition, we suddenly reached working temperatures of about 20-30 °C higher. At the same time, the mechanical and optical properties of the joints were not always ideal at the beginning. However, the technological features of lead-free solders have considerably improved over the past decade, and both the reliability and appearance of joints are mostly at a very good level. The biggest technological minus, which will not be overcome very soon, is the higher melting temperature and hence the higher thermal stress of the components during soldering.
How is it with melting temperature and why do tin-based solders, but without lead, have it usually higher?
Well, it's very interesting. Most interesting is the fact that sometimes alloys used for soldering have a lower melting point than the elements from which the alloy is composed. For example, pure lead has a melting point of 328 ° C and a tin of 231.9 ° C. However, the Sn63Pb37 alloy has a melting point of only 183 ° C (!).
The common and known lead-free alloy Sn96.5Ag3Cu0.5 (so-called SAC305) has a melting point of 217-218 ° C, thus apparently missing the positive effect of lead in the alloy to reduce the melting temperature. For those looking for an explanation of this phenomenon, we recommend entering the words
"eutectic" and "phase diagram of metals" in the search engine.
Why is the melting temperature sometimes referred to as an interval rather than a single specific value?
Again rather an interesting thing. If, for example, we find the melting point of 183-190 °C in the table for the Sn60Pb40 alloy, it means that even at temperatures as low as 183 °C, the metal appears to be liquid, but there is one large BUT – there is still a significant proportion of undissolved crystals. The whole metal dissolved only after heating above 190 °C and it is essentially the minimum temperature that the brazed joint should achieve in order for the resulting bond to have the desired quality. Metallurgy specialists, please excuse me, this is, of course, very simplified explanation, but I believe it’s sufficient for clarification.
Only with so-called eutectic alloy (metal ratio) is this interval so narrow that the melting range is essentially one temperature (not an interval).
Flux or why solder fumes during soldering ...

You may have sometime got in touch with (especially those born earlier) a flux-free solder wire. If you tried to solder it, the result was probably more than bad.
In fact, there is almost always at least a microscopic oxidized layer on the metal surface which prevents the good spreading of the solder. Even if the joint is perfectly clean before soldering, at the temperature at which it is commonly sold, a thin oxide layer is formed almost immediately. At the same time, the solder is also being partially oxidized, producing slag which further deteriorates the bonding properties.
To remove the tiny oxide layer, prevent oxidation during soldering, and ensure the best wettability, that is, the spreading of the solder, these are the main tasks of the flux, nowadays contained in almost every solder wire.
Historically, the main and still frequently used main constituent of flux is rosin, a substance obtained from the coniferous trees resin.
Thus, colophony is a natural material, with a relatively pleasant (for some people, even irresistible) fragrance. Colophony solder residues are not corrosive and may remain on a PCB. However, during soldering, the colophony is fairly smoke-rich and its residues are only harmless in a relatively dry environment. In a humid environment, they are subject to hydrolysis and can be slightly corrosive.
Manufacturers have gradually come up with many other modified colophony-based fluxes but also based on different resins or fully synthetic compounds. Colophony-based fluxes are still popular and have their place, but many synthetic fluxes that overcome the properties of colophony-based types are also available on the market.
We always find the exact flux specification in the technical sheet of flux or solder wire that the flux contains and is practically always described either according to DIN EN 29454-1 (eg type 1.1.2), J-STD-004 (eg ROM1) or according to standard DIN 8517 (eg F-SW26). In this example, type 1.1.2. roughly corresponds to type ROM1 or also F-SW26.
Where do we come across the fluxes?
Fluxes are typically contained in the solder wire in the range of about 1-3.5%. Of course, they are also available separately in liquid form and, to a lesser extent, in a gel-like or pasty form suitable especially for repairs.
To a large extent, liquid fluxes are mainly used in wave soldering. In the usual manual adding of a few THT components on a board already equipped with SMT components, the flux is usually not required as it is already contained in the solder wire.
It is worth mentioning that many fluxes also contain halides, especially those designed to solder not completely clean surfaces and to solder thicker joints (e.g. motor terminals, alternators, etc.). Halides have considerable "cleansing" and wetting properties, but at higher concentrations, they can be corrosive, hence the halide content is always easily identifiable from the classification of the flux.
Fluxes normally have different market names, e.g. HS10, KRISTALL 400, TELECORE HF 850, etc. In terms of both effect and process properties, there may be considerable differences between fluxes of the same classification but from different manufacturers. You can read more about the fluxes and their labeling on our website in our article
"Find the Right solder for you".
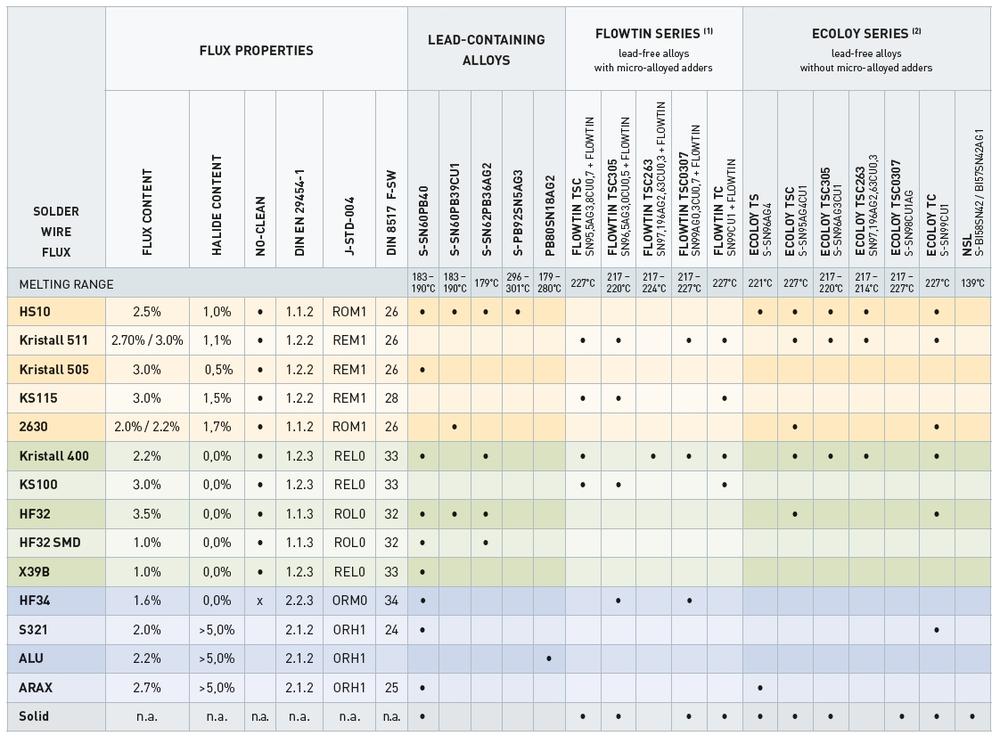
How is the flux information reflected in the solder name?
After reading these lines, it is clear that the full name of the solder wire always consists of the (commercial) flux name and the alloy composition, possibly the percentage of flux, such as KRISTALL 400 Sn96.5Ag3Cu0.5, 2.2%
Are all soldering wires spattering in the same way?
As we know, the hand-soldered PCB is usually contaminated with flux residues contained in the solder wire, as many fluxes are spattering several centimeters around the joint. However, there are already various types with low spatter fluxes on the market. "Low spatter", low smoke, as well as a small amount of translucent and non-tacky residues. Among widely known belong for example Kristall 400, Kristall 511, Trilence, Telecore HF 850 and others.
So we have a suitable solder, let's solder ...
Having a suitable solder and clean (non-oxidized) surfaces (component outlets) are essential prerequisites for good connections. Understandably, there is still a technological "minimum" that we should follow to get the perfect result.
Soldering station
In principle, it is "just" enough to be able to rely on the tip to have the temperature that we have set with as little deviation as possible. At the same time, the heat transfer from the heater to the tip should be as good as possible. In practice, these seemingly simple requirements are only satisfied by the quality solders from reputable manufacturers. Especially - the best heat transfer to the tip and then to the soldered joint is really quite a challenge.
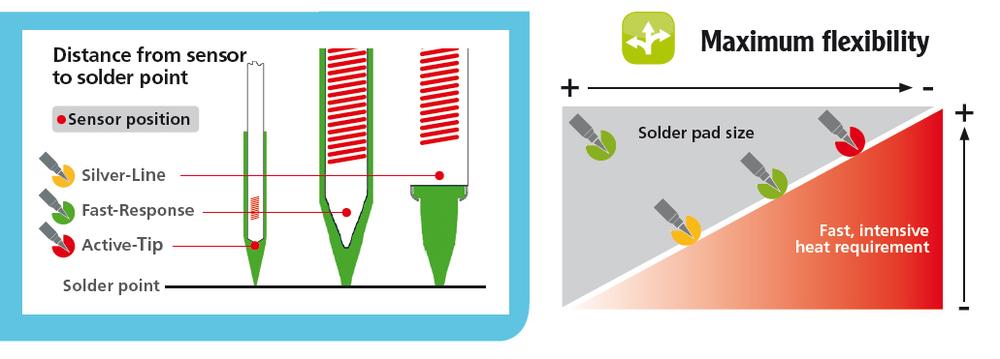
Why is it often so difficult to overheat a connection, even though the 380’C is on the display, which is about 150’C more than the lead-free solder temperature?
You may know the answer - because of low power, or more often - because of the insufficient heat transfer from the heating element to the tip and then the joint. The copper area around the joint, perforated holes, PCB material, outlets are all the mass that the tip must heat over the solder melting temperature and, moreover, they are like miniature coolers, with fairly good heat dissipation during soldering.
The heat transfer from the heater to the tip is the feature, which we can´t influence, but a suitable choice of soldering station and handles may help. Every serious manufacturer, such as in our company well-proven Weller, offers a comparison of its models and the selection table according to the size of joints.
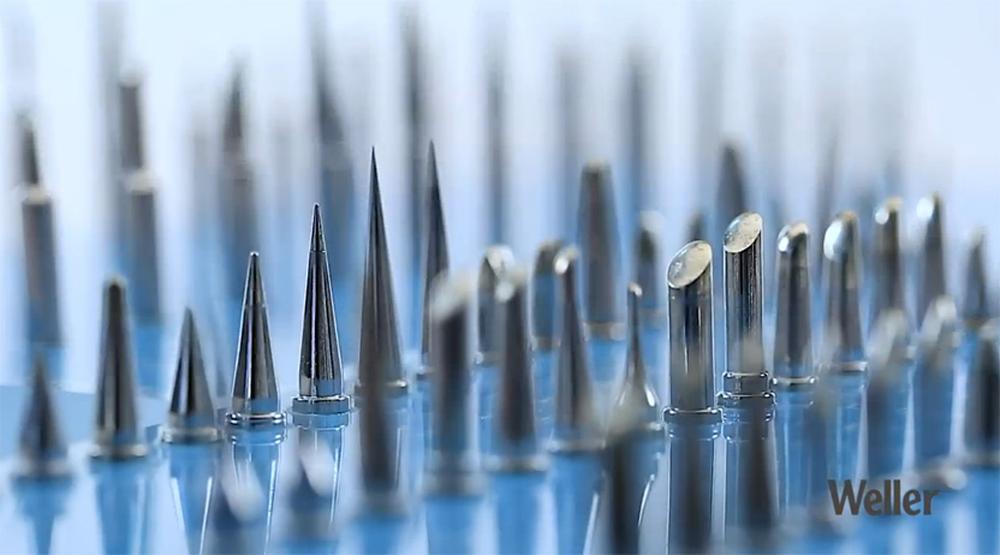
But what we can influence is choosing the right tip. In principle, the tip should be approximately as large as the soldered joint. In other words, it should be as large as we are able to use for a given joint. The better the heat transfer from the heater to the tip, the lower the temperature can be used. And this is a great advantage as we´ll show below ...
From a physical point of view, the best heat conducting properties are featured at the short and thick tip. Of course, the pike itself can be relatively thin, so it can be easily used e.g. to solder 0603 or 0402 SMT parts.
This is perhaps the most important rule when choosing a soldering tip. Practice shows that usually, the best choice is a short conical tip with a relatively thin flat chisel-shaped pike. An example of such a tip is, for example, type LT A.
Why is it preferable not to bake the tip too much?
As you know, even the same sized joints have a significantly different heat requirement. Usually, the worst are ground connections with a large copper surface around, with plated through-hole connections (so-called vias), especially in multilayer boards.
Thin and long tips usually do not help in such cases, as they cannot bring enough heat for demanding joints. Therefore, the operator often "helps" himself by setting a high temperature. Temperatures above 380-400 °C are considered a high temperature for long-term soldering. At these temperatures, the tip and solder on the tip oxidize very quickly, needing to be cleaned relatively often, and the life of the tip, as well as the heater in the handle, is significantly shortened.
At the same time, if the operator wants to "make life easier and to increase productivity", and he solders larger THT joints as well as miniature SMD components (with the same tip) without changing the tip temperature, small connections with little heat demand are exposed to unnecessarily high-temperature shock.
In contrast, the thicker and shorter tip, along with the good heat transfer technology from the heater to the tip, allow the temperature of 330-360 °C (sometimes lower) to be used for the same joints, while the lifetime of the tips and heater is significantly higher. The tip does not oxidize so quickly, so we do not need to clean it so often and the components experience smaller temperature shock. And, as a bonus, we also have a lower smoke and flux spread from the solder.
Why do we need to clean the soldering tips?
If we have a new tip and we touch the solder wire with it, the solder will usually spread beautifully throughout the tip. After some time of soldering, a portion of the point that does not touch the joints will usually be covered with a layer of oxides and flux residues, and the area on which the "solder" is held is gradually smaller and smaller.
In an extreme case when the entire tip is already oxidized, we cannot keep the solder on that tip. Although it is able to melt the solder, the solder jumps away from it as if it was impregnated…
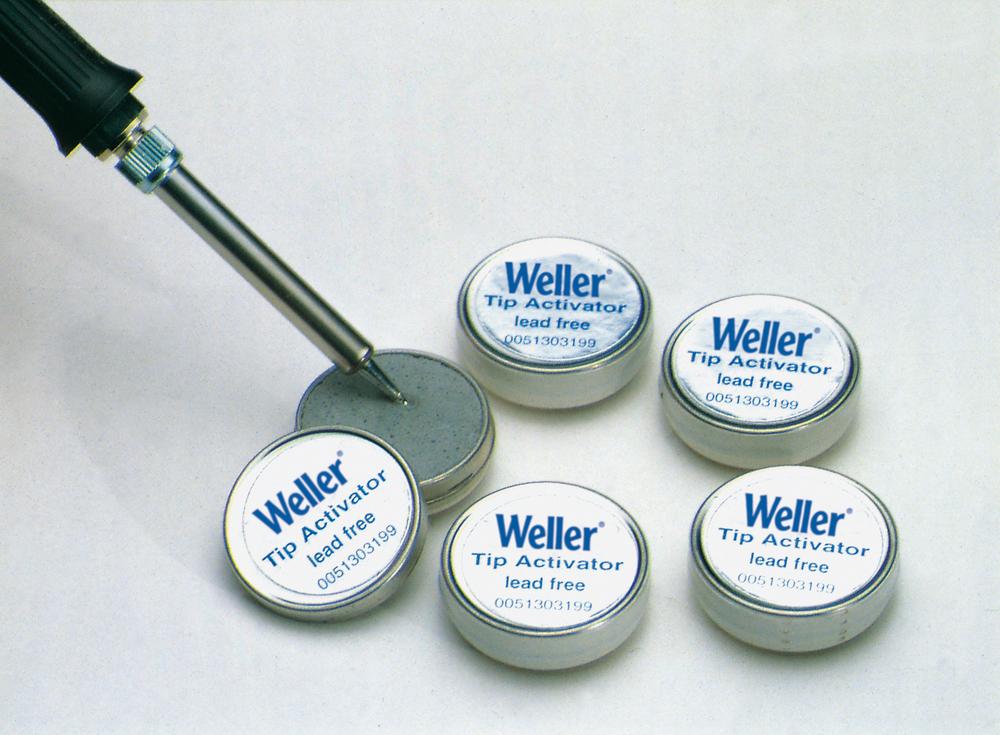
So we have to cleanse the tip. at first, only gently, preferably in a dry way in brass wool, which is usually part of the solder handle holders. Alternatively, only in a very slightly moistened sponge.
If this is not enough, the big help is the so-called tip regenerator, e.g. Weller tip activator, which cleans and tins the tip in one step.
However, even these tip regenerators operate only to a certain degree of pollution. If the tip is very dirty, only gentle and careful mechanical cleaning will help (there are also special fine brushes and abrasive stones, e.g. Weller WDC 2 kit ).

The core usually consists of copper and a layer of iron and then nickel. If the surface layer is damaged, or it even has a miniature recess in the tip, nothing will help and it needs to be replaced.
It is worth noting here that the thickness of the nickel layer and the tip construction are quite different at various manufacturers and in the vast majority of cases, the original manufacturer's tips have the longest lifetime.
Can I somehow prevent tip oxidation?
It is not possible to completely prevent it, but it can be significantly reduced. A simple and very effective method is to keep a little solder on the tip. This means that at any break in soldering when putting the handle into the rack, but not turning off the solder or switching to standby mode, it is good to apply a piece of solder to the tip. This solder will deteriorate within a few minutes but will perform its service as tip protection. Thus, before soldering, it is sufficient to wipe the tip in a brass wave and we have a clean tip with good wettability.
Also, having a clean tip is a big plus with regard to the above-mentioned heat transfer, since a dirty tip that holds the solder on only a small surface at the tip has a significantly smaller contact surface for heat transfer from the tip to the joint.
How long should I heat the circuit board?
A beginner and an amateur usually don´t care about time (length) of soldering and they have no problem to solder one joint for even up to 5-10 seconds. Of course, it's already quite a long time. At the other end, we usually find a pay-per-action operator, alias paid for the number of completed boards in a given time. These professionals often tend to shorten the time to a minimum, even below 1 second, usually at the cost of very high working temperatures, shortened tip and solder life, and moreover making a high-temperature shock to the components. As a result, however, such a joint is also of lower quality in terms of technology.
True professionals already have their own well-proven process and among you - readers, you will surely find a technologist from an EMS company, who has this issue managed to the last detail. For those less experienced, we can say that the recommended length of time for the tip to touch the joint is about 1.5-3 seconds.
If it is necessary to heat the connection considerably longer, there is usually a low set temperature, or more likely an inappropriate tip/power for the given joint.
If we look at a typical temperature/time graph for reflow soldering, we will find that SMT components can withstand quite a lot. And especially if we work mainly with SMT components, we can say that they can be more stressed by the temperature shock from the too hot tip (extremely steep temperature rise of a component in a short time) than a little longer soldering at a reasonable temperature.
What if I can't get enough heat even from a short and thick tip?
Obviously, in that case, the heat supplied from the solder handle/station is not sufficient. In other words, I need a more powerful station/handle.
In practice, for example, there is quite a big difference between typical 80W tools (such as Weller
WSP80) ) and 120 / 150W tools such as e.g.
WXP120.
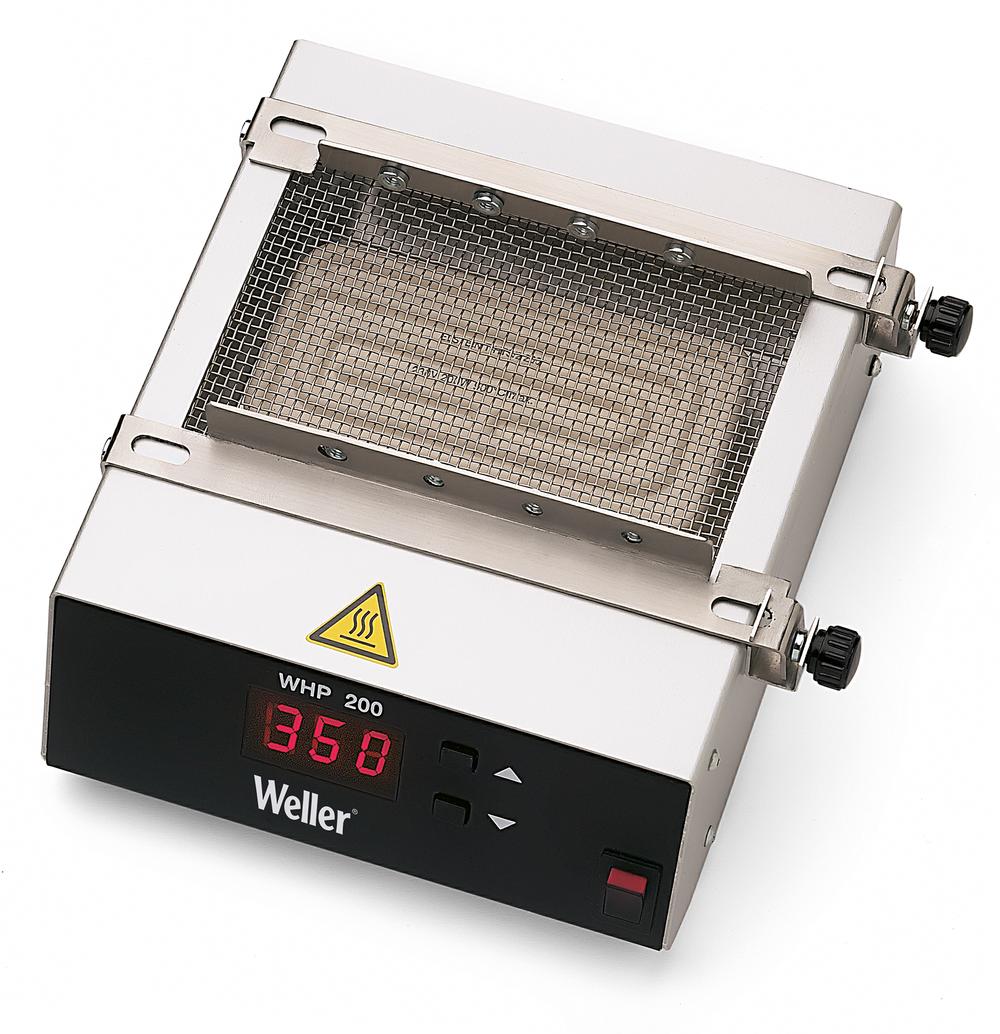
However, there is another known helpful device – the (bottom) heating plate. Thanks to the heating plate, we can heat the whole PCB to a certain temperature, which is still fully safe for other components on a PCB and consequently considerably reduce the need for the soldering tool power.
If we only heat the board to 100-120°C, we find that suddenly we can also solder earth-joints with a large area of copper around without problems.
In addition, the heating plate reduces the thermal shock of components, making it a very convenient accessory for manual soldering.
Can we do anything more about the lifetime of tips and soldering station?
Yes. If the soldering iron allows it, we recommend using any power saving mode (temperature reduction mode) while not soldering.
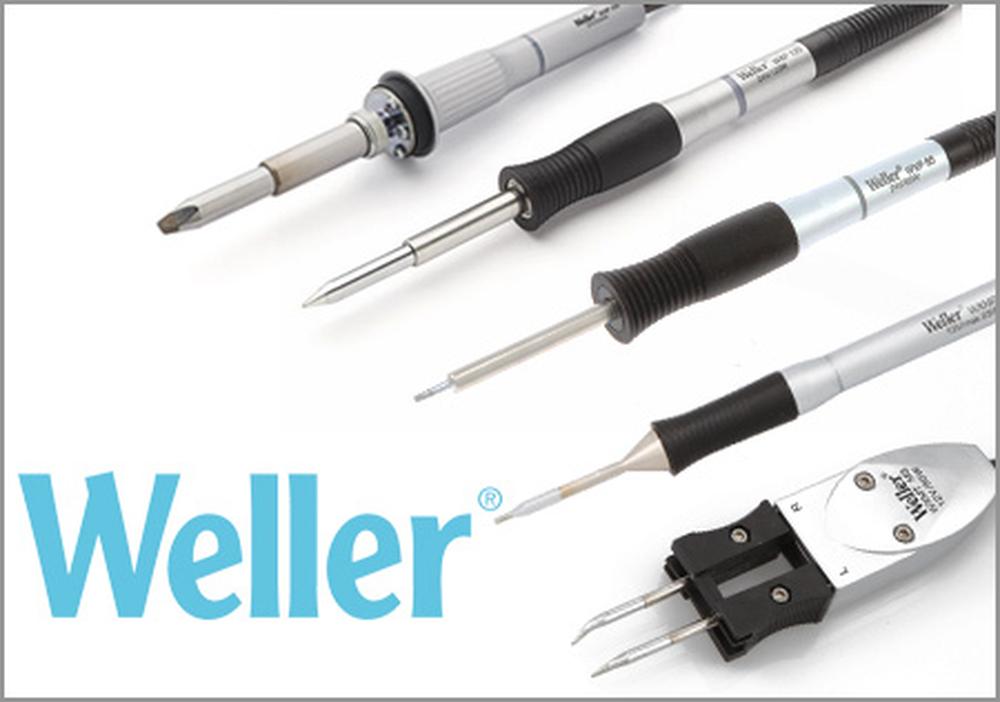
When we, for example, reduce tip temperature during a break to 150 °C, we, in fact, eliminate the formation of oxides during solder inactivity, while maintaining a sufficiently high temperature that the rise to about 350°C will be considerably faster than if we started from room temperature.
Some soldering irons use power monitoring to go into power-saving mode, some have a microswitch stand (or such a stand can be purchased, for example, WDH10T), and have a state-of-the-art motion sensor in the handle (for example, the entire WX handle series and Weller WTP90).
In principle, if we meet these basic assumptions, we are well on track to reach reliable joints:
- choose a suitable solder with good metallic composition as well as content and type of flux
- solder only clean and non-oxidized surfaces/outlets
- if the soldered surface is not ideal, it is possible to use more aggressive flux, but it will most likely be necessary to rinse the residues from the PCB
- use quality soldering station with reliable temperature measurement and good heat transfer from the heater to the tip
- use the largest and shortest tip usable for a given type of joint
- in many cases, the heater plate (bottom heater) is almost a miracle aid for soldering problematic heat-demanding joints
- original manufacturer's tips are in the vast majority of cases better and more economical as a result of their longer life
- do not use excessively high soldering temperatures to compensate not ideal tip selection
- keep the soldering tip clean and always tinned
We believe that our insights will help you solder even better than before. If you have other questions that we have not mentioned in the article, we will be happy to advise you at info@soselectronic.com or we can train you directly as in the case of our customers.
“By training, we have gained a real overview of how individual manual tinning activities are linked. Demonstrations - causing too high temperature, too low solder temperature during tinning was a good example for our employees, and despite our long experience in tinning, we have been given a different perspective on tinning and therefore we hope to improve our performance process. ”Qess s.r.o.
“The operators were fully satisfied with the form and content of the training. Thanks to the training we managed to guide all the employees through soldering, operation, and maintenance of soldering stations. In our reports, we have seen a decrease of scrap due to cold junction and short circuit. We have a lot of new staff since your visit and we are considering taking up this training so that we have the whole team back on one standard.” GE Energy Slovakia s.r.o.
Source:
http://www.soselectronic.com/articles/weller/practical-advice-for-quality-and-efficient-hand-soldering-2297